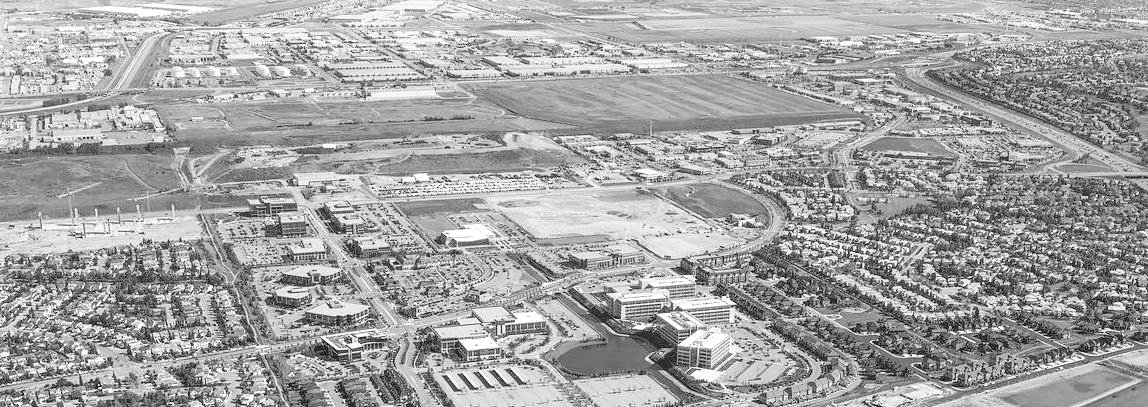
Low-Carbon Fuel Production
The Low-Carbon Fuel (LCF) will be shipped to third parties and used to generate power or heat.
Production of LCF at the ECCO facility does not involve any chemical processes, burning, or incineration of any materials.
The following is an overview of the Landfill Reclamation and LCF production process:
-
The viable materials recovered from the landfill will be unloaded onto the tipping floor inside the MRF, at which time a loader will place the materials onto an infeed conveyor leading to the first shredder. The initial shredder utilized in the Low Carbon Fuel (LCF) production process is a powerful size reduction machine designed to shred construction and demolition debris into smaller, more manageable pieces, about 18 inches (45cm) or less. This first step in the LCF production process ensures the waste materials are properly prepared for further processing, improving the efficiency and quality of the final fuel product.
-
Following the shredder, the materials enter a vibratory pan to spread the shredded Construction and Demolition material across its width so the materials are evenly distributed as they enter the ballistic separator (ballistor).
-
The smaller pieces of material then proceed through a Quality Assurance and Control process (QA and QC). Materials are distributed across two wide conveyors and audited by ECCO staff to remove any materials not designated for inclusion in LCF. One conveyor contains 2-Dimensional materials such as unrecyclable plastics and one conveyor contains 3-Dimensional materials such as Grade B Wood (OSB, MDF or Plywood). Examples of materials not designated for use in LCF include, metal, PVC pipe, Grade A Wood (dimensional lumber), and/or vinyl siding. Grade A wood is recovered for recycling into landscape mulch, metal is sent to a local third party recycler, and PVC/vinyl siding are examples of residual materials ECCO will send to an approved landfill facility.
-
Following the QA and QC process, both conveyors feed the materials into the fuel grinder. The fuel grinder takes the combined 2D materials (plastics and small pieces of paper or carboard), 3D materials (Grade B Wood), and remaining material from previous operations and grinds it to 2 inches (5cm) or less, producing the final fuel product.
-
As smaller material exits the fuel grinder it enters a disc screen responsible for ensuring the quality of the final fuel product, separating materials greater than 2" in size from those less than 2” and returns the larger materials to the grinder for further size reduction. With its precise screening capabilities and quality control measures, the disc screen ensures all fuel materials are less than 2" in size, consistently producing a uniform and high-quality LCF.
-
Last but not least, the LCF is loaded onto 53 foot walking floor trailers and tarped before proceeding to end users.
The finished product is 2 inches or less in size and includes a mix of materials such as Grade B Wood (OSB, MDF, Plywood); unrecyclable plastics; small pieces of cardboard, paper, or box board; textiles; carpet and underlay; and/or shingles. The mix of materials is a “recipe” based on the requirements of the end user but often looks like wood chips with the other materials mixed in as per the end users specifications.
A small portion of unrecyclable residuals (approximately 10% of all materials processed) from the MRF will be loaded into covered trailers for removal to an EPA Approved landfill for proper disposal.
click to enlarge